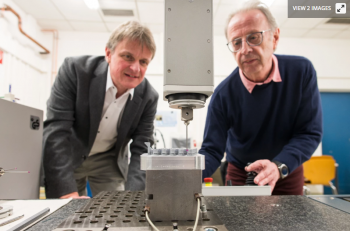
Although it's certainly possible to 3D-print metal objects, such items can't always be formed down to the sub-millimeter precision required for certain applications. A new technique, however, allows them to be infinitesimally tweaked after being printed.
Developed by scientists at Germany's Saarland University, the process utilizes a vibrating, downward-facing probe-like tool that dispenses an electrolyte solution (made up of aqueous salt) from its tip.
That tool is maneuvered into position, so that the liquid makes contact with the surface of the 3D-printed metal part in a target location. A high-voltage electrical current is then run through the solution, traveling from the tool and into the object. This causes minute particles of metal to fall off of the item's surface.
By varying the duration of the pulses and the frequency of the vibrations, it's possible to finely control the amount of metal that's being removed. What's ultimately left behind is a smooth-surfaced object that is accurately shaped down to a few thousandths of a millimeter.
So far, the technology has been successfully tested on relatively complex parts that were 3D-printed out of metals such as aluminum, titanium and steel.
"Our technology for post-processing additively manufactured metal parts offers a cost-effective means of producing high-precision functional surfaces for applications where extremely tight tolerances are crucial," says the lead scientist, Prof. Dirk Bähre. "It enables large numbers of parts to be post-processed efficiently and economically."